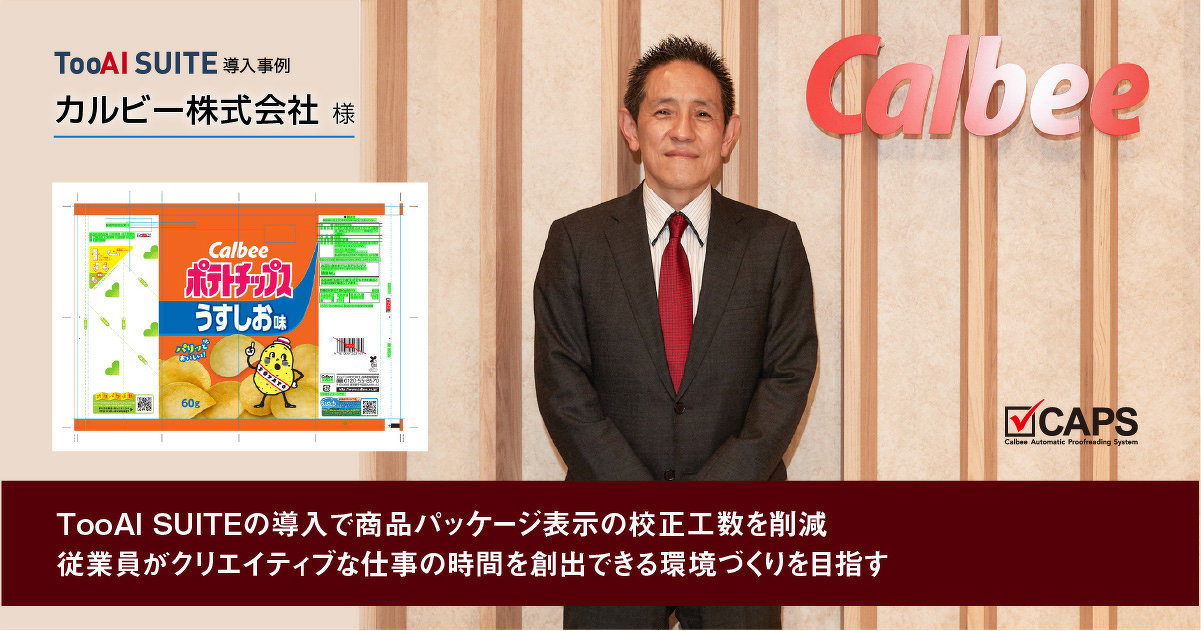
- 人の目による校正は精神的にストレスを感じている従業員もいた。
- 校正作業の効率化を進め、クリエイティブな仕事の時間を創出したい。
- 正解がある表示のチェックは100%任せられるシステムが必要だった。
- システム開発に必要な表示ルールをTooと並走して策定。
- チェックしたパッケージは500点を超え、未だバグ0件で稼働中。
「ポテトチップス」などじゃがいもを原材料とする商品をはじめ、「フルグラ®」といったシリアル製品などを製造・販売するカルビー株式会社様。商品パッケージの校正業務を効率化し、本来の業務に集中できる環境づくりを目的にプロジェクトを立ち上げ、パッケージ・ドキュメント制作の校閲や検査などを自動化する、AI/RPAソリューションTooAI SUITEを導入されました。導入の経緯や効果を、DX推進本部 DX推進部 部長 森山正二郎様に伺いました。
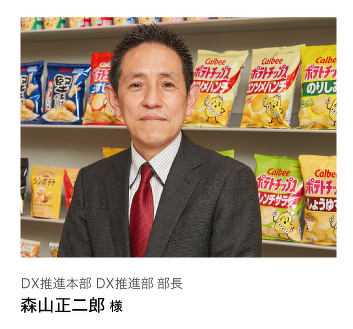
ITの活用でパッケージ校正作業の効率化と更なる精度を求めていた
カルビーは今年で創立73年を迎えますが、創立以来「私たちは、自然の恵みを大切に活かし、おいしさと楽しさを創造して、人々の健やかなくらしに貢献します。」という企業理念のもと、品質にこだわりを持って新たなマーケットを創造するユニークな商品・サービスを提供し続けています。
さまざまなお客様のニーズにお応えするため数多くの商品を発売しており、包装形態も多岐に渡ります。我々のプロジェクトは、これら商品のパッケージ表示の校正に関する問題解決に取り組んでいます。
パッケージ表示は、商品の特徴や原材料、アレルゲンといった、お客様にとって非常に大切な情報であるとともに、食品の法令順守という観点からも絶対に間違いがあってはならないものです。万が一表示ミスが起きてしまうとお客様の健康被害に直結してしまいますし、ブランドの信頼を失いかねません。そのため間違いのないように何重にもチェックをかけていますが、ほとんどが人の目によるものでした。そのプレッシャーから、精神的にストレスを感じている従業員もいました。
表示の間違いを修正する作業はとても重要ですが、本来の私たちの仕事は、より良い商品を生み出して、お客様に喜んでいただくことだという思いがあり、校正作業に膨大な時間を費やしている現状に疑問を感じていました。一方で、昨今のIT技術の発展は目覚ましいものがあり、こうした課題をITの力で改善できないかと考え始めたのがきっかけでした。
正解がある表示に関しては100%チェックを任せられるTooAI SUITEの導入を決定
〜情報収集からコンセプト作り〜
このような悩みを抱えている会社は他にも多いのではないか、先進的な技術を学ぶことができるのではないかと考えて、まずは食品会社やIT企業などにインタビューをおこないました。そこでわかったのが、どの企業も多かれ少なかれ同じような悩みを抱えていて、カルビー同様に人の目によるチェックに頼っているということです。この中で、完全ではないが表示チェックをおこなう効果的なツールを使っているという情報を得たのがTooさんを知るきっかけでした。
プロジェクトを立ち上げるにあたって考えたことは、パッケージチェックという大事な工程の一部にシステムチェックを入れることで、安全をしっかり担保しつつ、チェック者の負荷を減らし、ミスの流出リスクを減らすことでした。コンセプトは、「パッケージを入稿する前に、お客様にとって大事な原材料表示やアレルゲン表示といった情報は入稿前原稿の段階でチェックして、もし間違いが発見されたら必ず修正して入稿する。そうでなければ入稿してはいけないことにする。」という極めてシンプルなものにしました。
〜現状のワークフローを理解し重要なポイントを押さえる〜
我々の悩みをそのままぶつけ、一緒に解決できる技術を持った会社を探したのですがこれには難航しました。譲れなかった条件の一つが、ユーザである商品企画担当者、デザイン会社の運用をできる限り変えないことです。もう一つは、法令や社内ルール等で正解がある表示に関しては、システムのチェックに100%任せられることです。
世の中にチェックシステムは数多くありますが、そのほとんどが、人の目でチェックした後に使用する補助ツールとしての位置付けでした。読み取り具合によっては正確なチェックができなかったり、「〇〇%の信頼度で合っています」というように、安心して任せられないシステムが意外と多かったのです。チェック作業を減らして本業のための時間を1分1秒でも生み出そうという、我々のプロジェクトの目的に合いませんでした。
最終的に複数社のコンペをおこない、我々の要望に最も近かったのがTooさんの提案するTooAI SUITEでした。これはカルビーのパッケージの標準形をもとにシステム開発をおこなう提案で、確実にチェックできそうな期待感もあって、「一緒にやってみよう」という気持ちになりました。
システム開発に必要な表示ルールをTooと並走して策定
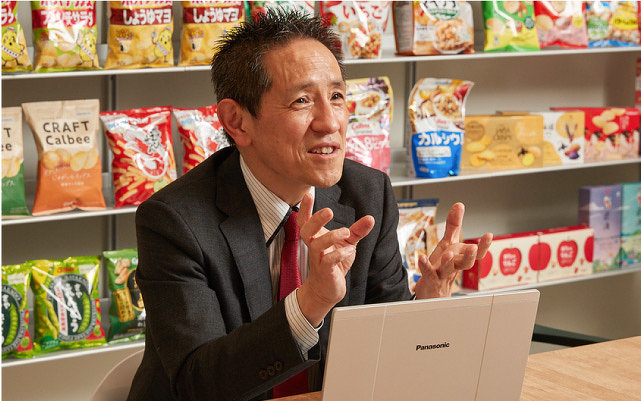
幸いなことにカルビーには、ポテトチップスなどのパッケージであるピロータイプの包装形態の商品に関して、「パッケージフォーマットガイド」という、パッケージ製作の標準形ルールブックがありました。また、パッケージのサイズや表示情報を細かく明記したカルビー独自の「パッケージ製作依頼書」を、弊社の商品企画担当者がパッケージデザインを手掛ける社外デザイナーさんに渡し、入稿前の原稿をテキスト情報の残ったPDFをデザイナーさんから共有フォルダーに登録してもらうという流れもできていました。この流れをできるだけそのまま利用して実現できそうだと考えました。
パッケージチェックに関わりの深い、商品企画、品質保証、消費者部門といった部門を横断するプロジェクトをスタートさせ、商品数の最も多いピロータイプ商品からの導入を計画しました。社内の仕組みやルールがあるから順調にいくだろうと当初は思っていましたが、いざ始めてみると非常に大変でした。特にプロジェクト開始早々、メインのポテトチップスの商品サイズが大幅に仕様変更になったことや、サイズバリエーションが予想を上回る多さだったことなど、想定外のできごとが次々に起こりました。
また、システムを作る上では細部にわたって「こういう場合はこう読み、これを合格として、これはエラーにする」と細かい定義をしていく必要がありますが、ルールが定まっていない部分も多く、改めてメンバーと議論を交わしてルール作りに奔走しました。そうしたさまざまな動きをしっかりとサポートしてくれたのが、Tooさんのプロジェクトメンバーでした。彼らの業務理解度は非常に高く、時には我々ですら気づかないような「表示ルールの死角」をしばしば指摘してくれて、本当に頼りになるパートナーさんだと感じました。
シンプルなUIで危険箇所やフォントサイズも直感的に判別できる
「CAPS」Calbee Automatic Proofreading System
2020年春、ようやくピロー包装の一部でシステムチェックの運用をスタートしました。スタートに際して、システムの名称もプロジェクトチームでアイディアを出し合って、これにしよう!と決めた名前が「CAPS」です。「Calbee Automatic Proofreading System」の頭文字をとったもので、社内では現在もこの名前で通っています。弊社デザインチームに所属するプロジェクトメンバーが、ロゴデザインも作成してくれました。
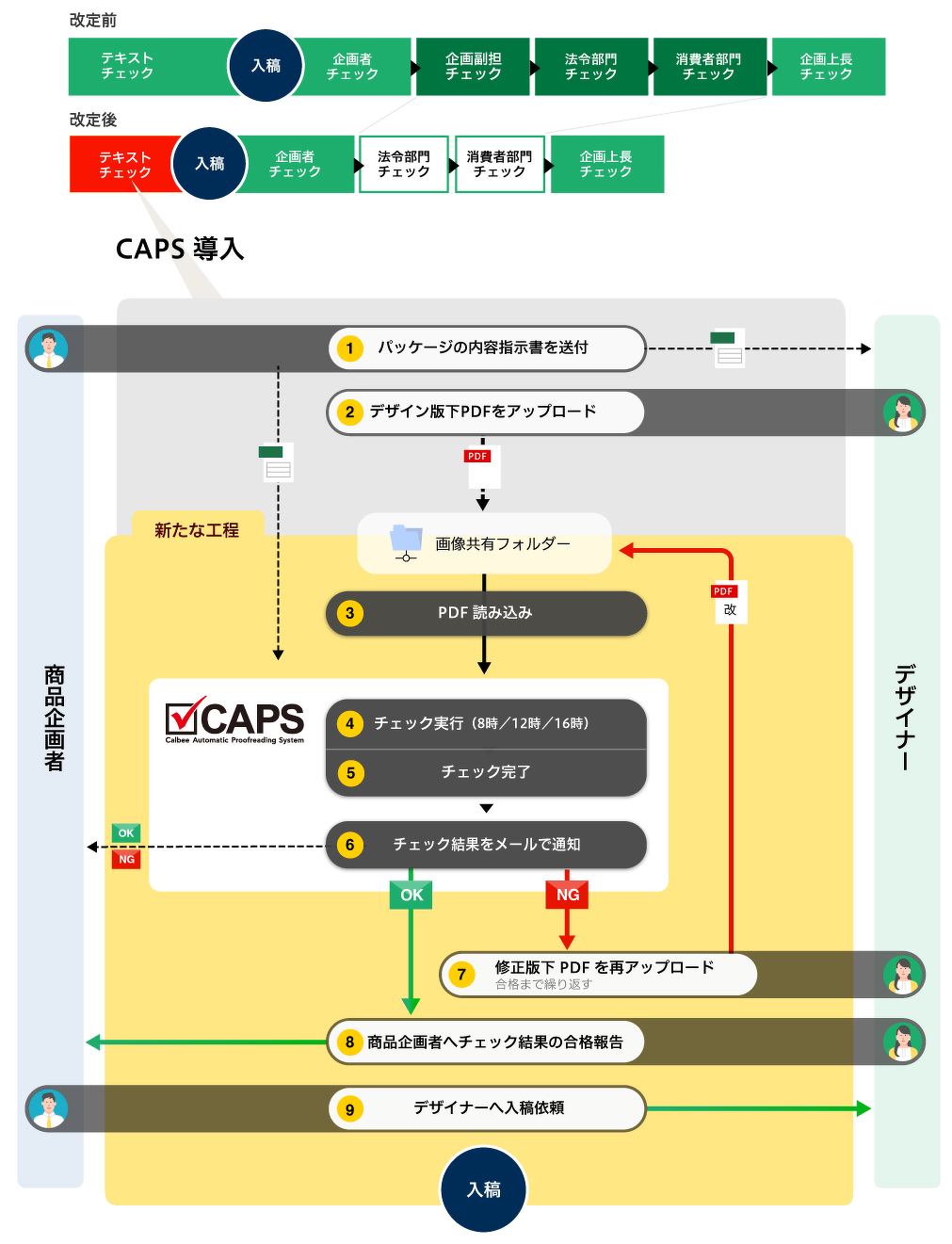
主な工数削減点
- 商品管理システム内のテキストチェック作業削減
- 企画副担当のチェック作業削減
- 法令部門副担当のCAPS対象項目のチェック作業削減
- 消費者部門のCAPS対象項目のチェック作業削減
CAPSの良いところは、まず操作がシンプルなところです。必ずしもITに強くないユーザであっても、やり方の説明を一度受けていれば、簡単な操作でチェック結果の確認までたどり着くことができます。また、チェックした結果も間違っている部分は赤く、注意しなければいけない部分は黄色く表示され、直感的に危険個所がわかるので好評です。
特にユーザが苦労していたのは、フォントサイズのチェックでした。以前は透明フィルムで作成したゲージを使い目視でチェックしていましたが、今はCAPSがルールに適合したフォントサイズかどうかを判別してくれます。この点は、企画者からもデザイナーからも非常に助かったという声をもらっています。
CAPSでのチェックが始まってから、デザイン会社さんから渡されたデザインの中には細かい単純ミスが意外と含まれていることがわかりました。もちろん未然に流出防止できていたのですが、これまでこうしたミスも人が目と手を使って確認し、差し戻し、訂正をして、間違いなく直ったかを再確認する……と気が遠くなるような作業をしていたかと思うと、パッケージチェックの作業は本当に厳しいものなのだな、とあらためて感じます。
CAPSでチェックしたパッケージは500点を超え、未だバグ0件で稼働中
これまでCAPSでチェックしてきたパッケージ数は500点を超えますが(2022年4月現在)、今のところシステムのバグは0件です。パッケージチェックにかかる人的工数ですが、CAPSチェックをおこなう代わりにチェック人数を見直すなどして、対象商品ではおおよそ3割ほど削減されたのではないかと思います。今後も運用の定着状態を見計らいながら、さらなる工数削減を検討していきたいと考えています。
デザイン会社さんの単純ミスもCAPS運用開始以降、減ってきたように見えます。修正点がデジタルで記録に残るため、ミスが可視化されることによる効果かもしれません。従来は間違いを指示したらその場で終わっていたのが、今はどの会社さんがどのようなところをいつ間違えたか、CAPSのチェック結果が蓄積されています。 ミスの傾向を掴むことで、適切な教育や指導が可能になり、社内やデザイナーさんたちに向けた事例勉強会も開催しています。
導入当初は、CAPSチェックという新しい取り組みに戸惑う意見もありました。業務の流れも変わりますし、CAPSでチェックされた結果の確認という作業は出てくるからです。しかし、CAPSによってミスが視覚的に分かるようになり、今はユーザーから「CAPSを通すことで安心できる」という声を聞くことも多くなりました。ようやく前向きに使ってもらえるようになってきたのではないかと感じています。
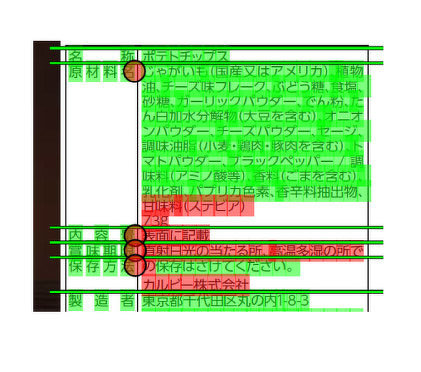
例)「項目名」の段にズレが発生した場合、
エラー部分が赤く表示されます。
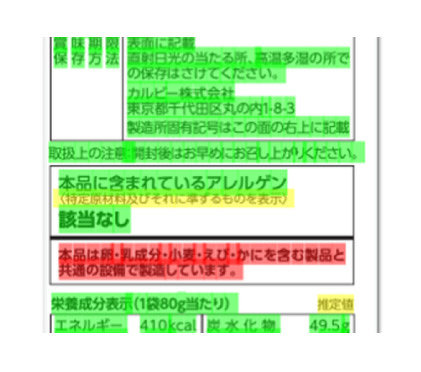
例)本来、長体としない文字があった場合、
その部分が赤くエラー表示されます。
CAPSの対象商品を拡大し、クリエイティブな仕事の時間を創出したい
現在は、CAPSでチェックできる商品の種類のさらなる拡大に取り組んでいます。まずこの春(2022年)、フルグラのカテゴリーについてのパッケージチェックについてCAPSを使った運用に切り替えました。さらに、スタンドパックとカップの包装形態の商品についてCAPSでのチェックができるように進めています。スタンドパックは、パッケージ表記のフォーマットガイドの標準形作りから始めました。ようやくその標準形ができた段階で、これを元にTooさんがシステム開発に取り掛かっています。
カップ商品については展開図が扇型になるため、斜めに表示された文字をチェックするという、これまでとは一段と難しいシステム要件があり、これを技術的にどうクリアするかが課題です。しかしTooさんであれば、この課題も解決してもらえると確信しています。
今後はカルビー内でCAPSを使ったパッケージチェックの運用をしっかりと定着させ、チェックにかけている人の工数を本来のクリエイティブな仕事の時間へ転換しつつ、表示ミスの流出リスクの削減も目指していき、お客様への安全安心レベルを格段にアップさせることができればと考えています。
さまざまなパッケージ表示を標準化し、それに従った原稿を作成することは、チェックシステムを採用するか否かに関わらず、表示ミスをなくすための第一歩だと思いますね。標準形に基づいたデザイン作成ができれば、TooAI SUITEの活用によって、カルビー以外の食品会社でも実用可能な気がします。導入までは決して簡単ではないかもしれませんが、興味があればTooさんに相談するといいと思います。
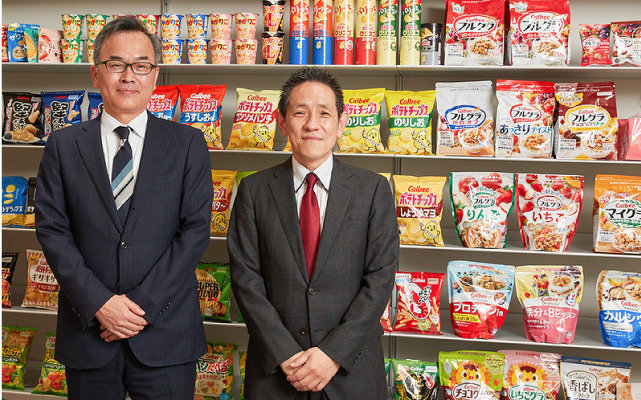
森山様(右)とToo 担当営業の古賀(左)
※記載の内容は2022年5月現在のものです。内容は予告無く変更になる場合がございます。
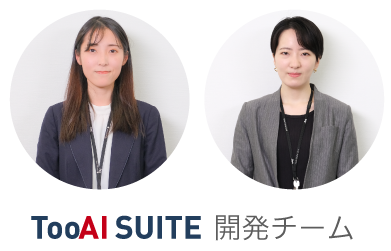